Slew bearing change-out is crucial for maintaining heavy machinery’s stability. This blog explores ASPEC’s assessment of jacking points, addressing compliance with AS 4324.1 and client specifications. We’ll address common pitfalls and solutions, ensuring safe design and operation, and how ASPEC’s approach minimises risks while maintaining operational continuity.
Background
Department of Mines and Petroleum (DMP) issued the Mines Safety Bulletin No. 103 relating to an incident involving localised deformation at multiple jacking points during the replacement of a reclaimer slew bearing. One of the main contributing factors was inadequate stiffening of the diaphragms adjacent to the jacking pads.
Following the incident, ASPEC was engaged to perform several structural investigations, including the analysis and remediation of the jacking points on various stackers, reclaimers and shiploaders to ensure compliance with AS4324.1 and the client’s specifications.
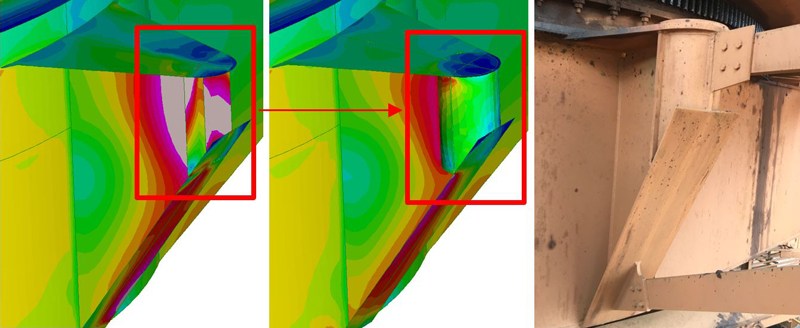
Figure 1: Example of Slew Bearing Change-Out Jacking Point FEA Analysis and ASPEC Strengthening Design
Common Issues for Existing Machines
ASPEC found common causes of non-compliant jacking points were:
- Design requirements not being clearly described in the technical specifications.
- No allowance for wind loads appropriate for the maintenance period.
- No allowance for jack load eccentricity and lateral design actions. This often results in inadequate stiffening of the plated structures local to the jacking points.
- The mass and balance of the as-built machine varied from the design balance.
- The stability of the superstructure whilst supported on the jacks did not meet AS4324.1 requirements.
AS4324.1 Design Considerations
AS4324.1 requires maintenance loads (X) be considered during any special maintenance operations, such as the replacement of slew bearings. However, AS4324.1 does not provide specific guidance on calculating jacking loads or allowing for jack eccentricity. Unless documented in the client’s technical specifications, it is often up to the designer’s interpretation to determine the appropriate jack loads that will result in a safe, robust design of the jacking points.
Some key points to consider when designing jacking points for slew bearing change-outs and other maintenance activities include:
- Calculate the maximum expected jack loads using AS4324.1 maintenance load combination II/4:
- Incorporate weight variation allowance of the structure in the analysis.
- Include wind loads experienced by the structure appropriate for the expected maintenance period.
- Include jack misalignment in the design.
- Eccentric loading from the jack will occur if the vertical load applied through the jack is misaligned or if there is a horizontal force applied to the top of the jack.
- Verify each jacking point with a jack working load limit (WLL) rating, clearly stating the maximum allowable jack eccentricity and any other procedural requirements.
- Confirm stability of the superstructure whilst supported on the jacks and include requirements relevant to the overall machine stability in the jacking procedure i.e. the machine position and maximum wind loads during maintenance.
- Allow for jack redundancy in the jacking procedure.
- Consider the use of two jacks at each jacking point. If one jack fails, the other jack is able to support the full load while the failed jack is changed-out.
ASPEC has an extensive experience in slew bearing change-out jacking points and other maintenance activities. ASPEC can assist clients with the following:
- Structural design reviews of jacking points on new and existing machines, including verification of working load limit ratings and machine stability during maintenance.
- Design of jacking point strengthening to existing machines to ensure compliance with AS4324.1 and client specifications.
- Development of jacking point design specifications for new machinery.
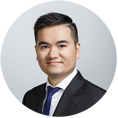
Anthony Nguyen is a Structural Engineer with over seven years of experience in technical engineering, structural inspection, risk assessments and project management. He is a Chartered
Professional Engineer and has been with Aspec Engineering since 2011.