Figure 1: Iron Ore Reclaimer (Left) and Stacker (Right).
Bulk materials handling machines face high failure rates, especially compared to static structures. ASPEC’s study investigates 68 machine failures in Australia between 1977 and 2020, revealing key insights into the rates and causes of these failures. This blog examines how wind, maintenance issues, and overloads contribute to machine breakdowns and how adherence to standards like AS4324.1 impacts these rates.
Stackers and reclaimers, such as those used for Iron Ore (Figure 1), are bulk materials handling machines. These machines are large moving structures that are constantly experiencing dynamic loads whilst in motion. Worldwide, their failure rates are higher than standard static structures like buildings.
ASPEC has collected data on sixty-eight failures of bulk materials handling machine that have occurred in Australia between 1977 and 2020. Bulk materials handling machines include stackers, reclaimers, stacker/reclaimers, ship-loaders, and ship-unloaders. The study conducted has identified two main aspects of these failures, the first being the rate of failure and the second being the cause of failure (e.g., wind, fatigue, overload etc.). Figure 2 shows the results of this study, demonstrating the number of failures (both partial and total) over a 44-year period.
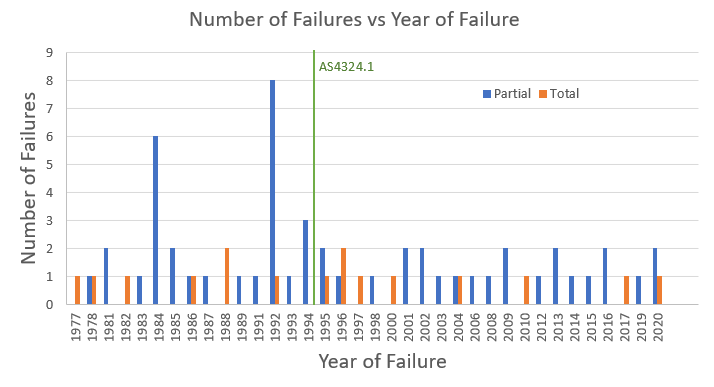
Figure 2: Number of failures vs Year of Failure for Bulk Materials Machines.
Partial failures are defined as failures that are not part of regular maintenance and require major repairs whilst total failures are defined as total collapse of the machine such that it could not be reinstated [3]. A substantial number of failures occurred prior to the introduction of Australian Standard AS4324.1 in 1995 [1]. Investigating the cause of machine failure for the recorded sixty-eight Australian machine failures demonstrates that of the total failures almost a quarter (24%) are attributed to wind events, with maintenance management and overload tying for second at 19% (Figure 3). Additionally, in collating this information it was found that 85% of the failures that occurred were on machines erected prior to the adoption of AS4324.1.
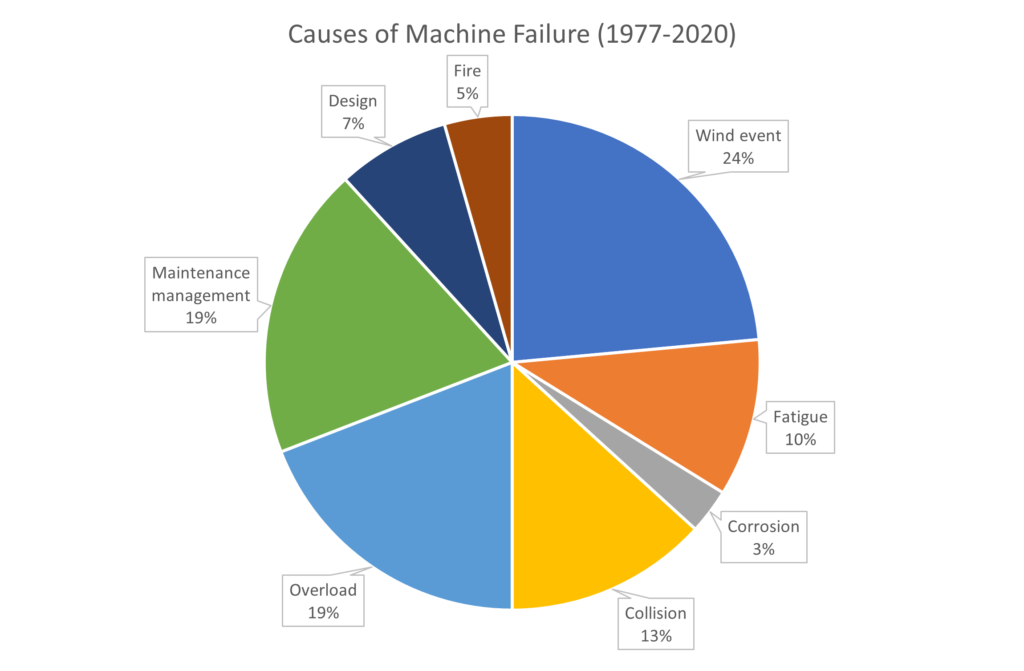
Figure 3: Cause of Failure of Machines between 1977 – 2022.
Figure 4 shows the cause of failure only for machines which have been constructed after the introduction of the Australian Standard AS4324.1 in 1995 which details design standards of mobile equipment for the continuous handling of bulk materials. Post-AS4324.1 failures due to wind account for half of all machine failures.
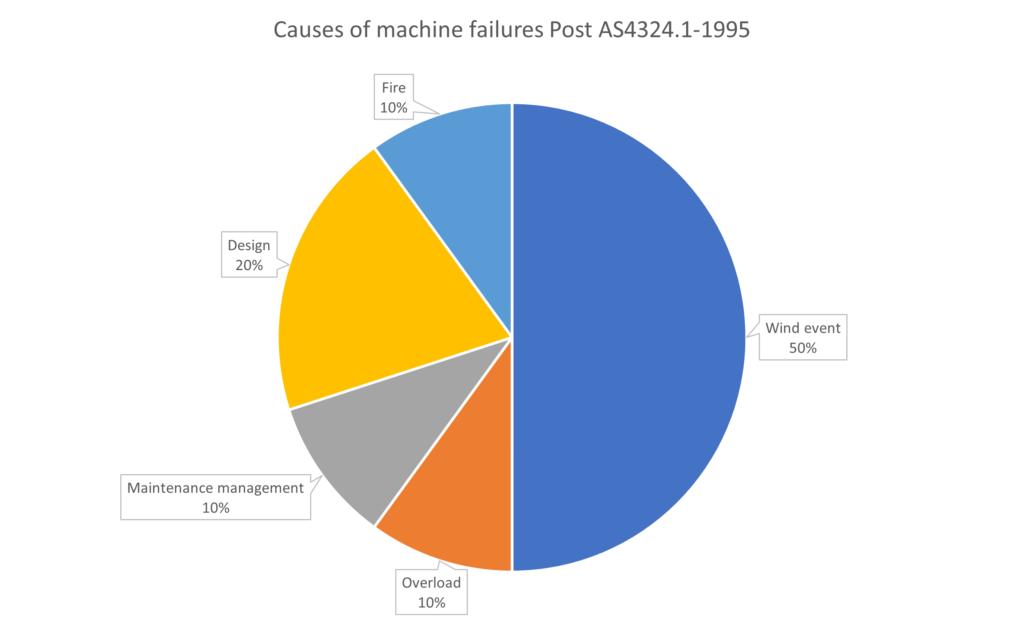
Figure 4: Cause of Failure in Post-AS4324.1 – 1995 machines.
The normal protocol for dealing with wind loads is for bulk handling operations to stop at a defined operational wind speed, usually 20m/sec or 22 m/sec. The machine then travels to a storm tie-down location where it is anchored and then able to resist the ultimate design wind at the site. The relocation wind is higher than the operational wind, usually 30 – 33m/sec.
Many of the wind failures have been due to thunderstorm events rather than tropical cyclones. A feature of these systems is that they occur as a localised cell or super cell and can happen with little warning. In one recent case the wind gusts went from less than 10 m/sec to 48 m/sec in 5 minutes. This is not enough time to stop loading and relocate to the storm tie down. Hence, if the site is susceptible to this type of event the machine needs to be able to anchor to the rails at any position along the track. The wind standard AS1170.2 [2] has also been revised recently and recognizes the effect of thunderstorms, particularly in regions away from the coast. Additions need to be made to the appropriate clauses in the AS4324.1 standard to safeguard against failures due to thunderstorms.
Figure 5 shows the long travel drive system and rail clamp on a ship loader at a bulk loading port. Brakes on the long travel drives and rail clamps can be engaged to resist forces when the machine is stopped. The designer needs to ensure that the combination of the long travel brakes and rail clamps have sufficient capacity to hold the machine in the event of a sudden storm event. Maintenance of the systems is important to ensure that the brakes and rail clamps remain in adjustment. Quite often one or more of the drives and brakes are removed for maintenance in the workshop and it is important that there is redundancy in the system to allow for such.
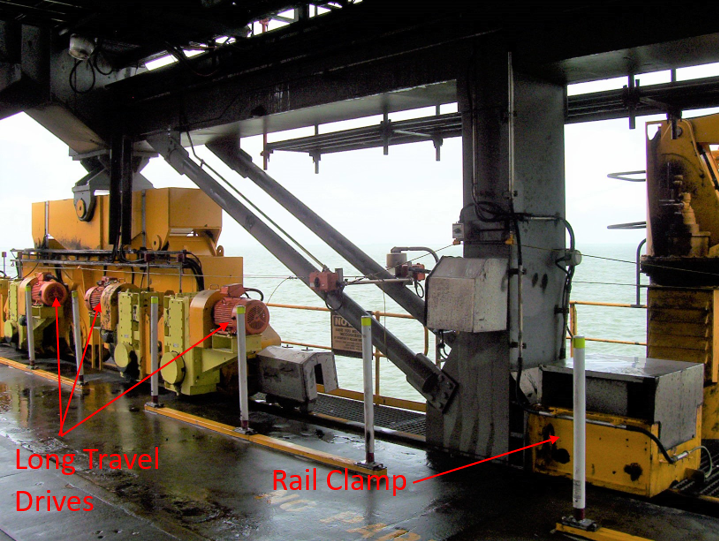
References
[1] AS4321.1 – Mobile equipment for continuous handling of bulk materials. Homebush: Standards Australia, 1995.
[2] AS1170.2 – SAA Loading Code – Part 2: Wind loads. Homebush: Standards Australia , 1989.
[3] R. Morgan and F. Gatto, “Defying Time,” World Coal, pp. 1–4, May 2002.
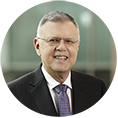
Richard Morgan is a Structural Engineer and Director of Aspec Engineering with extensive experience in bulk materials handling and ports. He is chairman of Australian Standards Committee ME43 for materials handling machines. He is a Chartered Professional Engineer.