ASPEC provided detailed engineering services for a major upgrade of Shiploader SL1 at Hay Point, including new boom, portal refurbishment and throughput upgrades.
SL1 is the oldest machine at the terminal, having been first commissioned in 1971. Prior to the most recent upgrades of the machine, SL1 suffered from major structural integrity issues as a result of extensive fatigue cracking of the main boom, resulting partly from the large number of shuttle and telescopic trim movements on the machine, and partly from legacy issues with structural detailing of the boom connections. These issues resulted in substantial downtime of the machine, requiring quarterly shut downs for structural inspections and repair.
These issues led BHP to embark on a major upgrade programme for the machine including: replacement of the main boom; installation of a new portal operators cabin and remote operations equipment to reduce risk to operators; an increase in machine throughput, operability and reliability improvements; functional safety upgrades; and structural integrity repairs including repainting of the machine.
ASPEC was selected as the engineering service provider for the project, and completed detailed structural, mechanical and electrical engineering design for the upgrade, in collaboration with a number of key industry partners.

The scope was successfully executed during major shutdowns in late 2020 and 2021, with an exemplary safety record of no lost time injuries. The project overcame several major challenges, which ultimately represented major highlights for the project. These included:
- Execution of a major brownfield upgrade during the peak of restrictions imposed by the COVID-19 pandemic. This presented a major logistics challenge, for the 150+ personnel involved with the project on site.
- The age of the machine and brownfield nature of the project, created major challenges throughout the design and execution of the project. Many of these challenges were mitigated through the extensive use of 3D parametric modelling and drafting throughout the design process.
- Capacity constraints of the existing berth and shiploader meant that tight weight control was required, despite the addition of new features, equipment and increased throughput. The machine is now operating well at a throughput that is 165% of the original 1968 design capacity for the machine – a testament to the success of this and past upgrades.
- The existing berth had very limited capacity for craneage. As a result, a large jack up barge was mobilised for the project, allowing for smooth and successful major construction lifts and assembly of the new boom.
- A reduction in operator risk exposure through installation of a state of the art portal cabin and cameras, moving the operator off the main boom, and away from potential harm due to ships collisions.
- A highlight of the project was the extent of stakeholder engagement throughout the design and execution of the upgrades, with on-site operators and maintainers providing valuable input into the final outcome.
ASPEC is proud of our involvement with BHP and key industry partners, in delivering another excellent project supporting Australia’s critical export infrastructure.
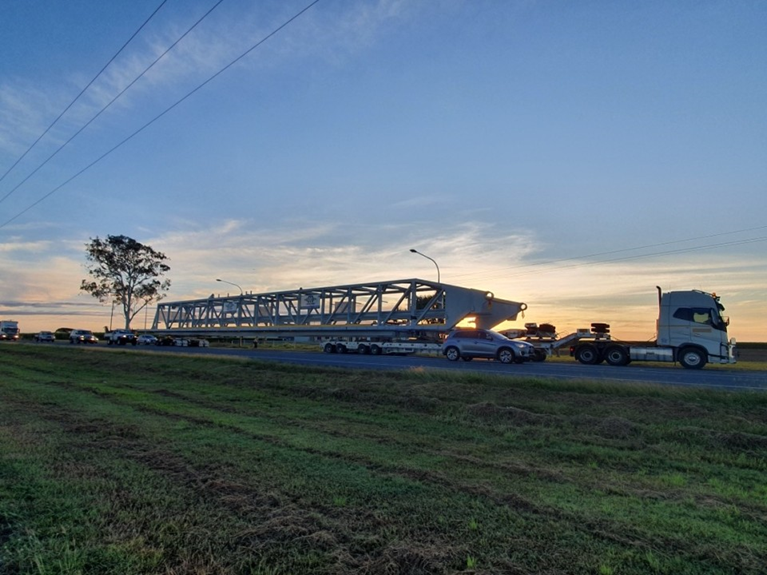
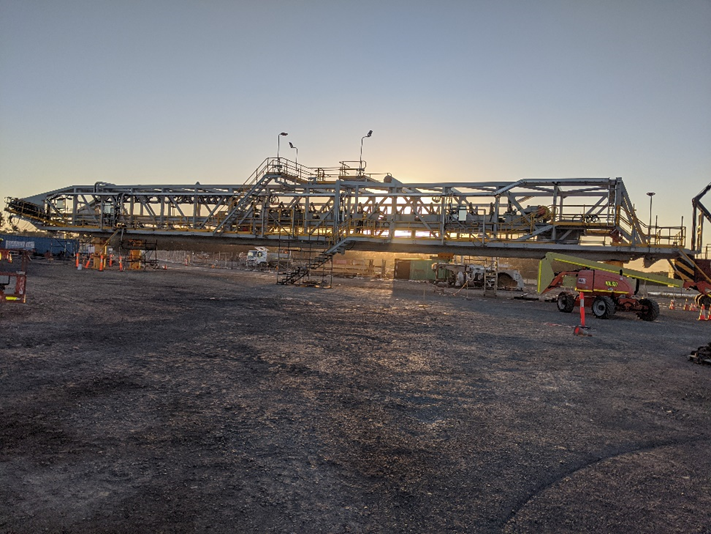
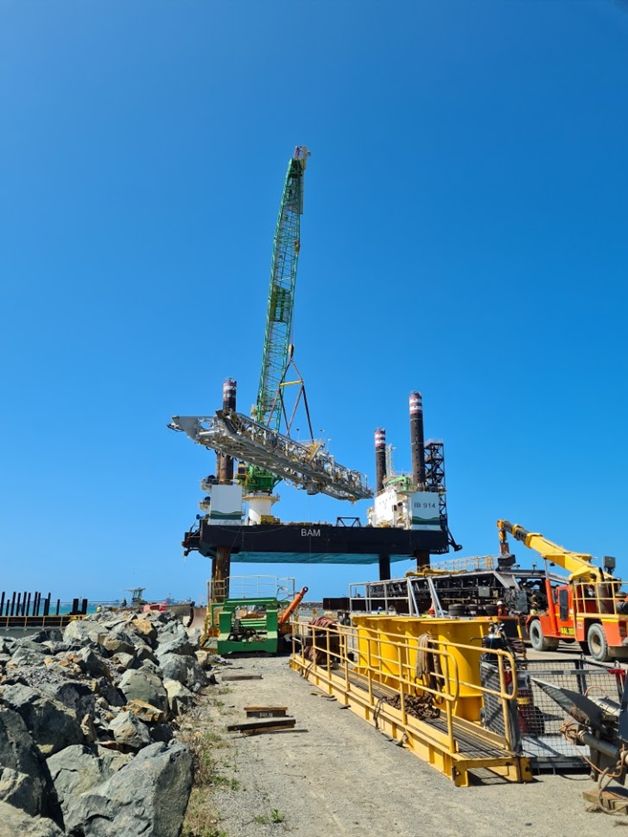
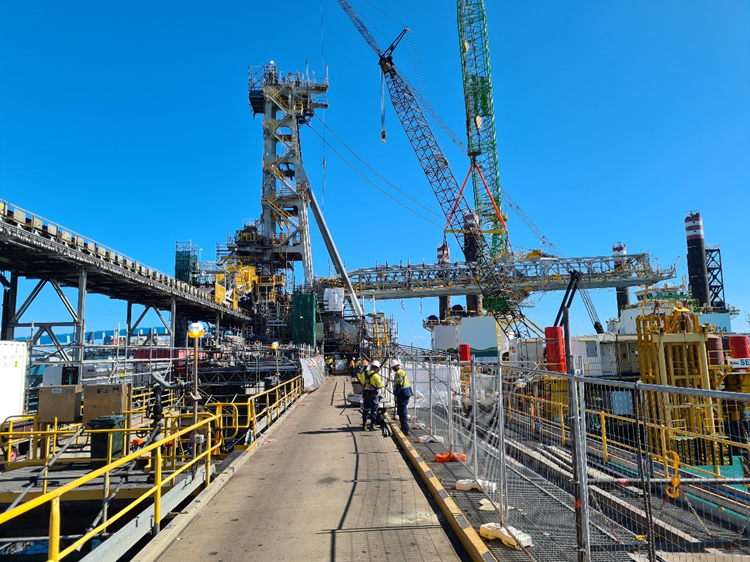
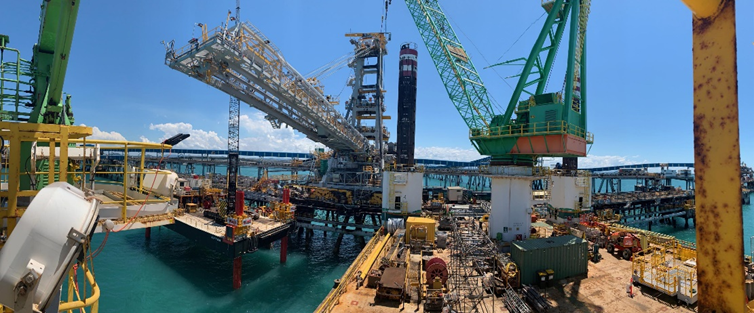
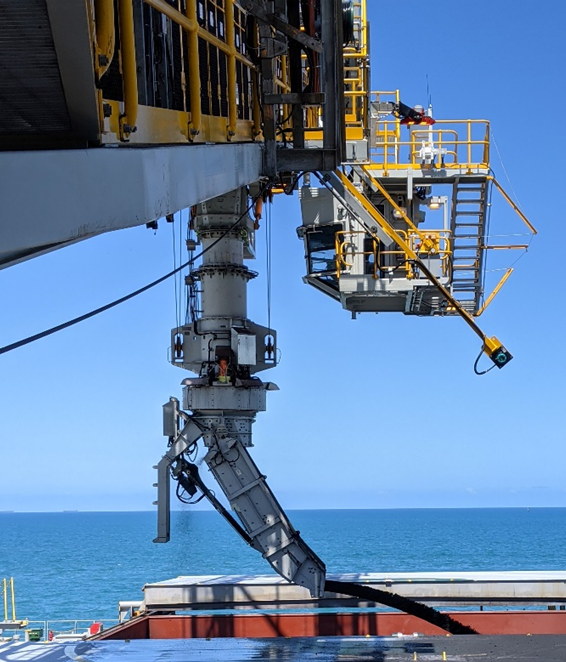
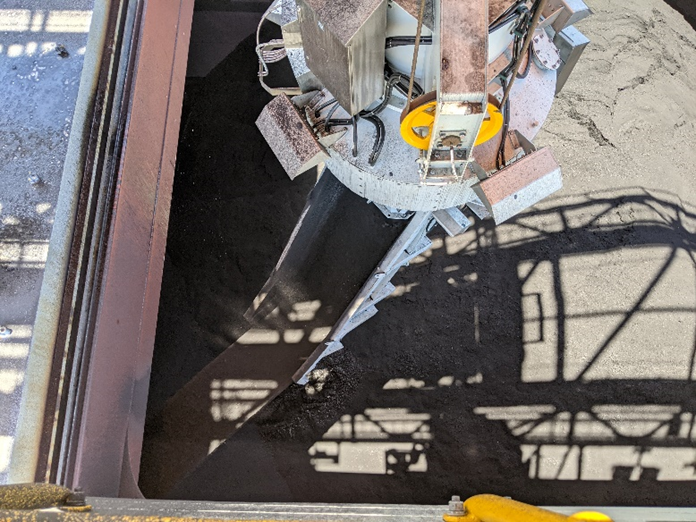
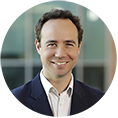
Adam is a lead mechanical engineer at ASPEC, with over 15 years experience in the heavy industrial and resource sector. Adam is a Chartered Professional Engineer with a PhD in the field of mechanical engineering. In his time at ASPEC Adam has worked on a wide range of projects and gained broad experience in the field of mechanical engineering, specialising in materials handling systems.