The introduction of 3D printed models has opened a whole new world for designers to visualise complex structures, bridging the gap between 3D digital models and tactile models, and providing a new complete approach and understanding of the challenges of a project and its processes. Aspec Engineering uses 3D printing to represent intricate designs, assembly processes and challenging repairs during the design process when the visualisation of complex models is essential for comprehending the task. Here are a few illustrative examples:
Investigative Replacement Design
The analysis and upgrade of a complex design for a series of impellers that had failed due to fatigue cracking on the trailing edges of the aerofoil fan blades. By utilizing 3D printed models, engineers and fabricators were able to collaborate and identify challenges in the manufacturing process, resulting in the development of a highly efficient impeller design that could withstand the centrifugal forces these impellers are subject to during operation.
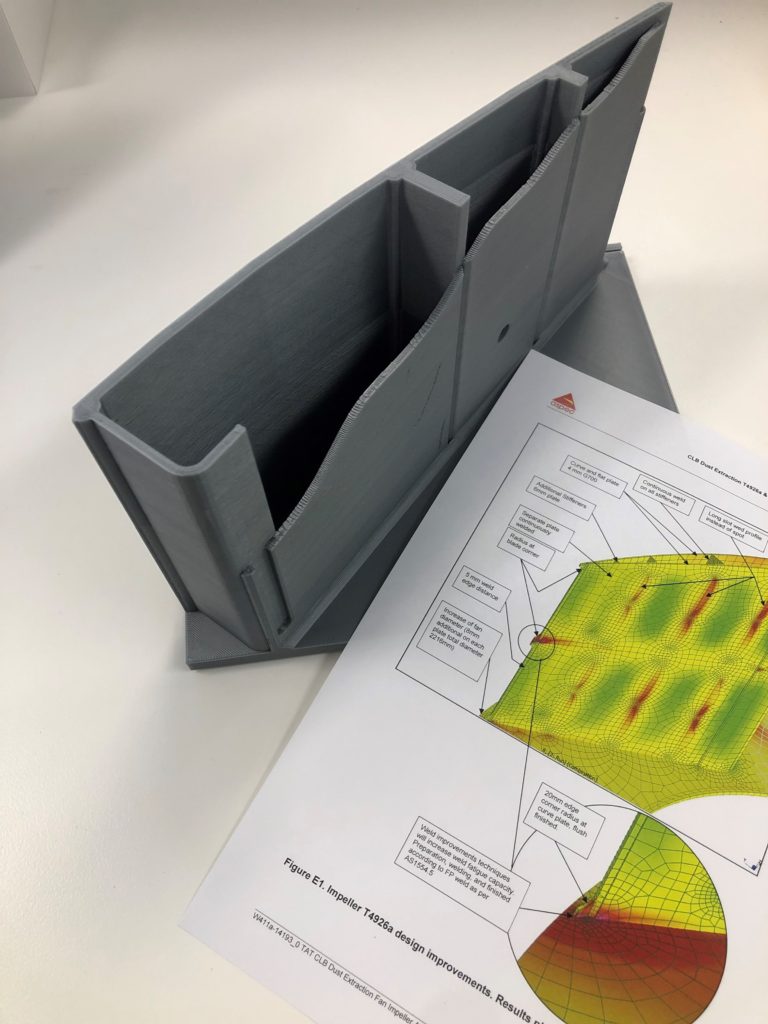
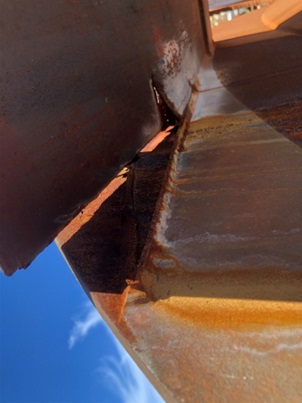
Figure 1: Upgrade of a complex impeller design that had failed due to fatigue cracking on
the trailing edges of the aerofoil fan blades.
The feasibility of constructing the new impellers can be assessed with the use of the 3D print models prior to the proceeding to the production stage, effectively minimizing production costs.
Accurate welding details are crucial for fatigue design, as incorrect details can result in significant failures. The use of 3D printed models allows for the precise replication of the required weld details for this project, facilitating their presentation in meetings with welders and boilermakers. This enables better communication and ensures that the intended weld details are clearly understood and implemented, reducing time, cost, and the risk of potential failures.
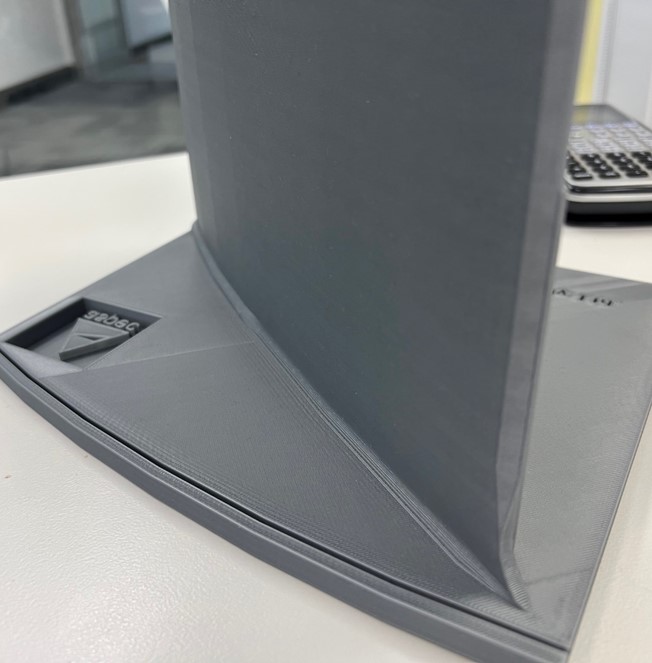
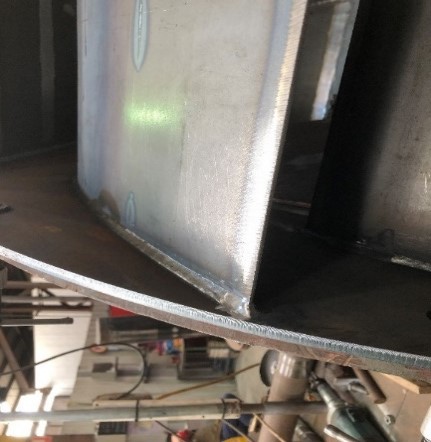
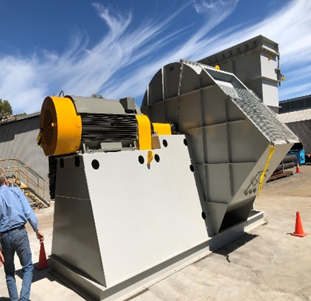
Figure 2: Welding detail improvements of impellers.
New Engineering Concepts
A new engineering concept for the jacket design to be installed as part of the new shipping berth at Port Hedland in WA, has unique challenges that can be visualized with the help 3D printed models and effectively communicated to the participants in site meetings.
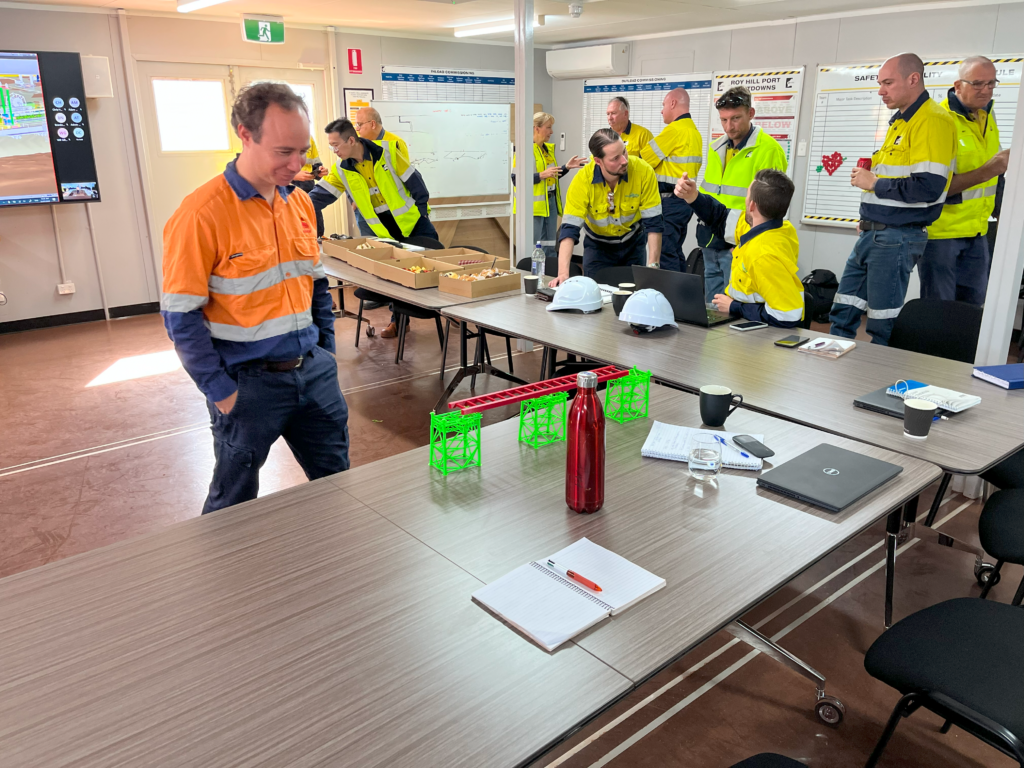
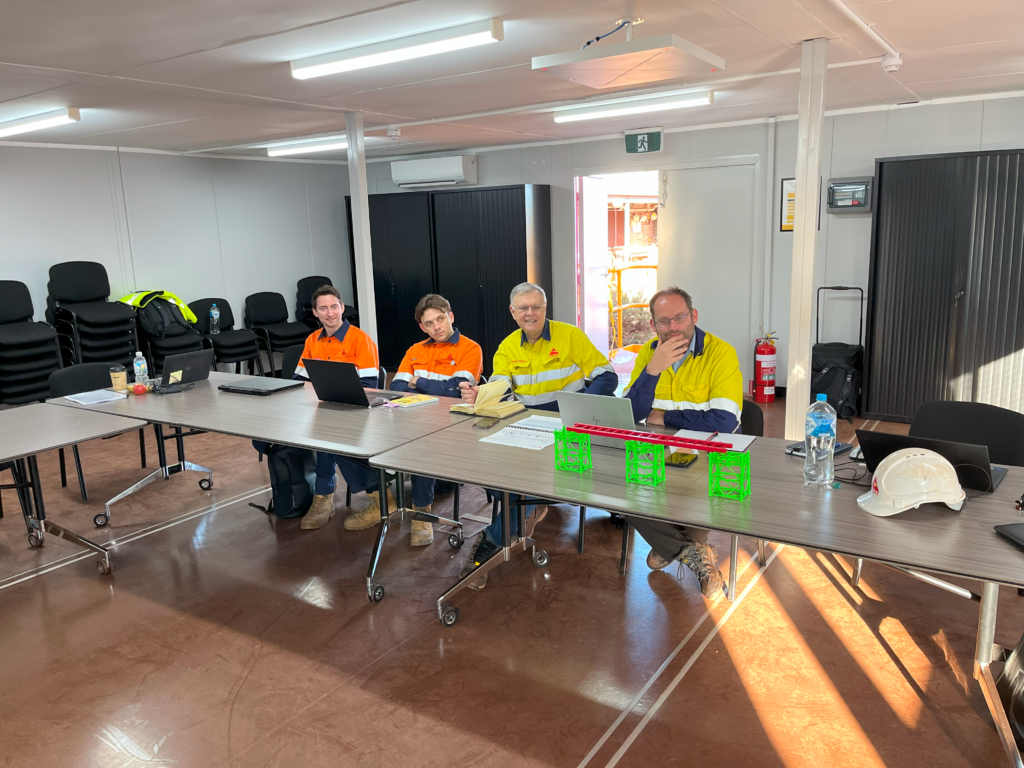
Figure 3: Aspec & Rendel team presentation at Port Hedland, WA.
The 3D printed model can be combined with a computer 3D model presentation and give a new approach to the project and easily identify conflicts or better strategies for the engineering process.
Repair Design
General 3D prints can significantly improve visualisation for site teams and fabricators of challenging repairs, resulting in improved planning and execution of critical repair works.
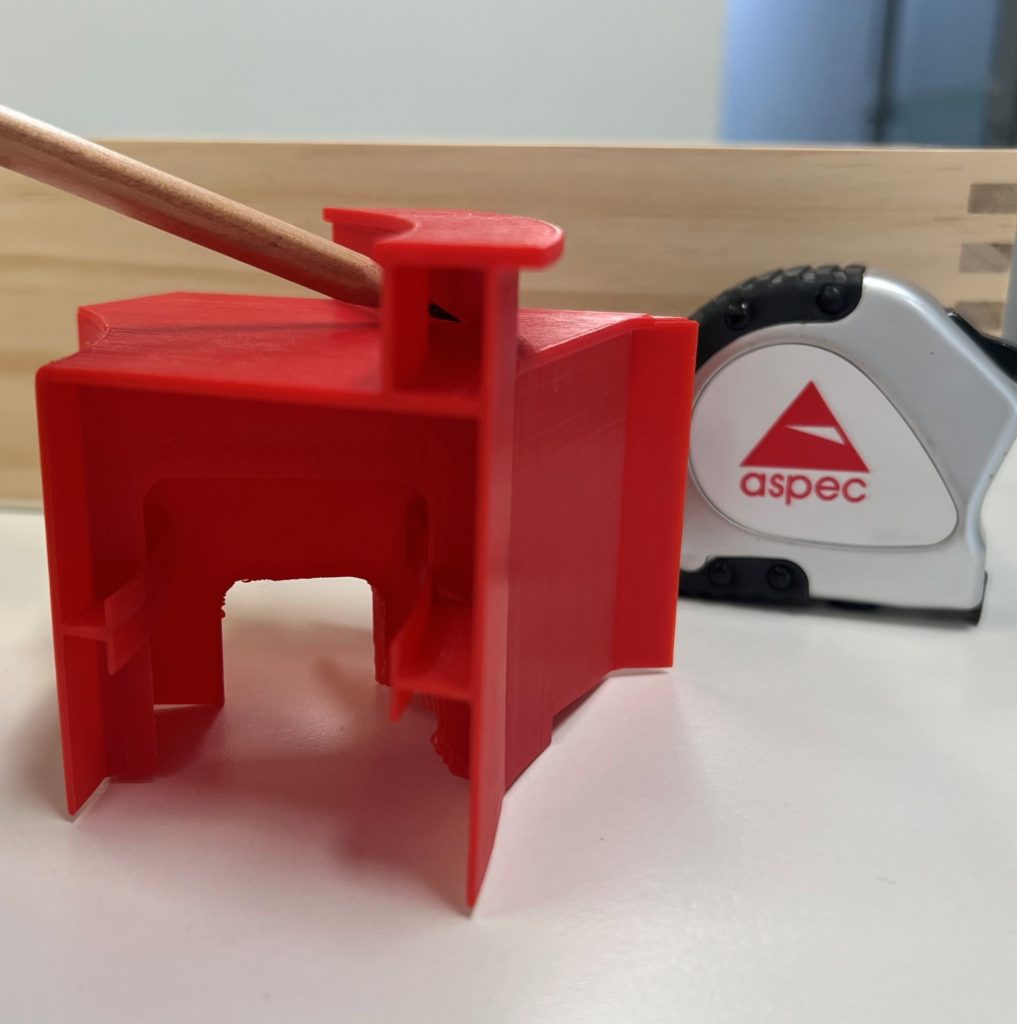
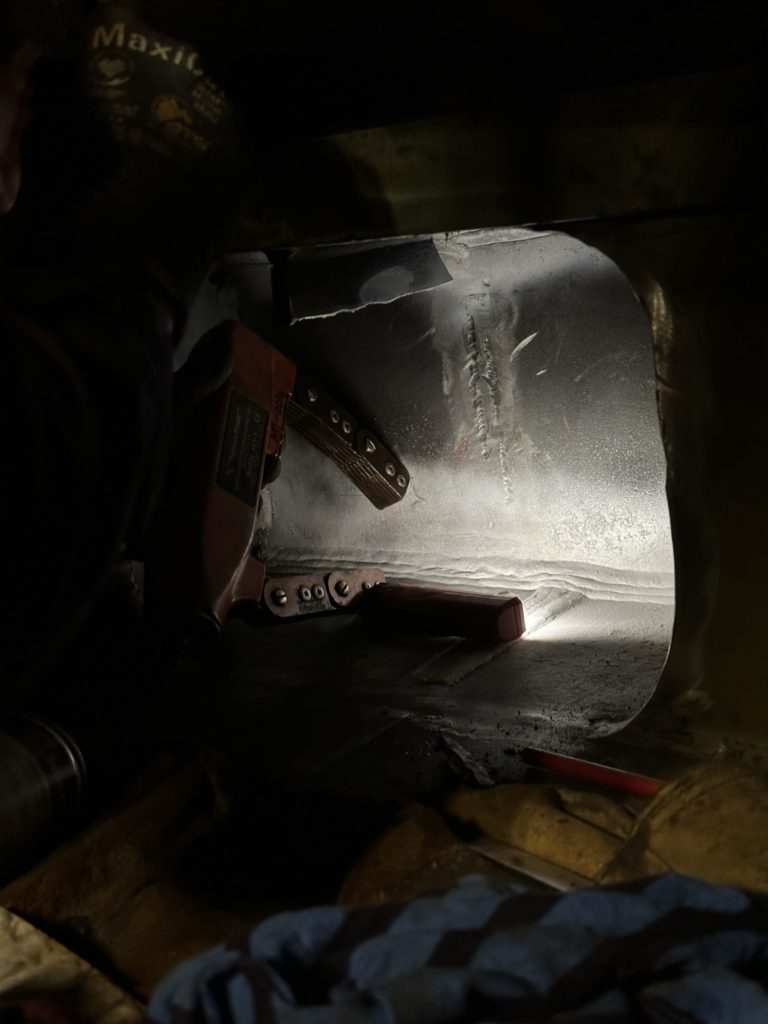
Figure 4: Circular box girder modifications to conduct crack repairs on a reclaimer at iron ore mine site in WA.
Conclusion
The use of this tool has key advantages allowing designers, engineers, and workers to effectively interact and share their ideas into the next design stages.
Overall, 3D printing is a revolutionising tool that Aspec Engineering is actively incorporating into the design process, offering exciting possibilities for innovation and collaboration. Its continued use is expected to increase and then pave the way for new applications and transformative approaches to engineering development in the future.
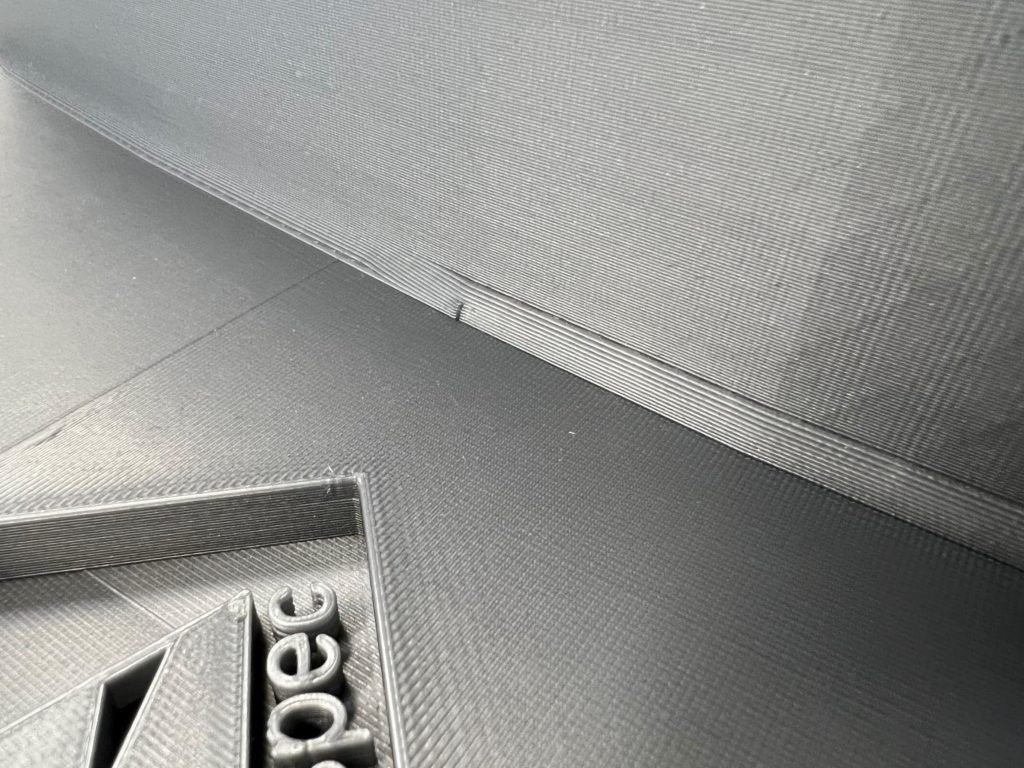
Figure 5: 3D print fatigue welding detail.
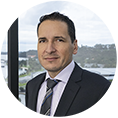
Edwin is a Structural Engineer at ASPEC’s Perth office. He has over 10 years of experience in structural design, inspections and manufacturing across several roles. He has been mobilised to work onsite within the mining and heavy industries sectors since 2005.