AS 4324.1 – 2017 sets the standard for designing mobile bulk material handlers like excavators and stackers. Recently updated to reflect new safety and efficiency standards, ASPEC partnered with Dr. W.H. Kang to test how these new guidelines hold up under real working conditions. This blog explores their findings and the real-world implications for equipment design.
AS4324.1 Mobile Equipment for Continuous Handling of Bulk Materials Part 1 is the standard for the design of mobile equipment for continuous handling of bulk materials such as excavators, stackers, reclaimers, ship loaders and ship unloaders.
One of the changes in the recent published AS4324.1:2017 from the previous version of the standard (AS4324.1:1995) is the revision of the limit state design (LSD) requirements that are compatible with the loading requirements in AS/NZS1170.0. The LSD method in AS1170.0 adopts partial load factors to take into account the different level of uncertainties in different load types, and AS 4324.1:2017 has adopted the partial load factors that are consistent with those in AS/NZS 1170.0.
ASPEC has completed a study with Dr W.H. Kang to evaluate the reliability of steel columns using load factors provided in AS 4324.1:2017[1]. The reliability model is based on the proposed probability distribution of design parameters (Figure 1) based on experience[2]. For example, it is assumed that majority of time the machine is doing 85% of design throughput (Live Load F, mean 0.85).
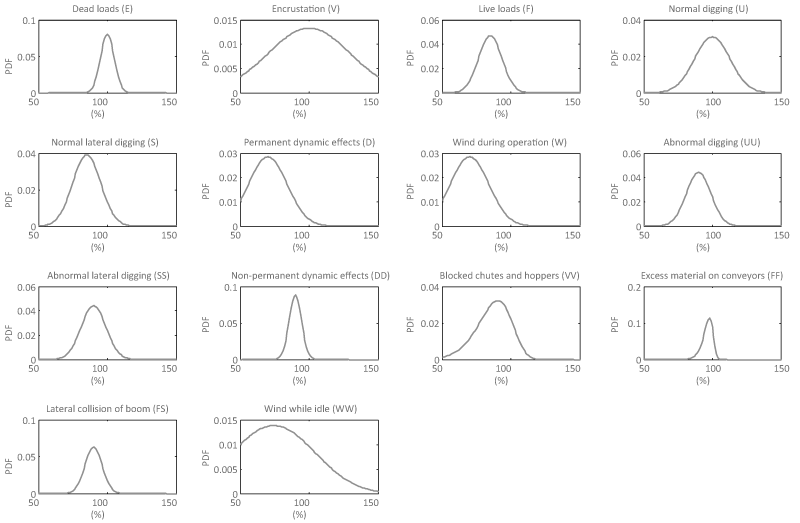
Figure 1: Probability Distribution of Loading Parameters in AS4324.1-2017
To verify the probability distribution of the design parameters, load distributions have been generated based on on-site load measurement data for the corresponding design parameters. The load data were acquired from 3 reclaimers, 2 stacker reclaimers, 3 stackers, and 1 ship loader for periods varying from 14 days to 3 months, using Supervisory Control and Data Acquisition (SCADA) systems: boom conveyor weightometer readings (throughput) for live load (F); bucketwheel drive torque reading for normal digging (U); and slew drive torque/slew speed reading for normal lateral digging (S). The details of the machines used for the study are as follows:
- 1850t Iron Ore Reclaimer, 57m boom, 14,850 tph design throughout
- 1150t Iron Ore Reclaimer, 46m boom, 4,125 tph design throughput
- 1100t Iron Ore Reclaimer, 50m boom, 9,000 tph design throughput
- 1050t Coal Stacker Reclaimer, 59m boom, 4,500 tph stacking & 4,800 tph reclaiming
- 1100t Coal Stacker Reclaimer, 60m boom, 6,000 tph stacking & 7,200 tph reclaiming
- 400t Iron Ore Stacker, 45m boom, 11,500 tph design throughput
- 350t Iron Ore Stacker, 33m boom, 4,500 tph average throughput
- 400t Iron Ore Stacker, 40m boom, 11,000 tph design throughput
- 650t Iron Ore Ship loader, 49m boom, 7,700 tph design throughput.
The load data was calibrated against strain gauge data and was found reasonably accurate. The comparison of these two sets of distributions for F, U, and S obtained from measured data and qualitative judgement is provided in Figure 2, and it was found that the proposed distribution of design parameters is more conservative than with the site measured data.
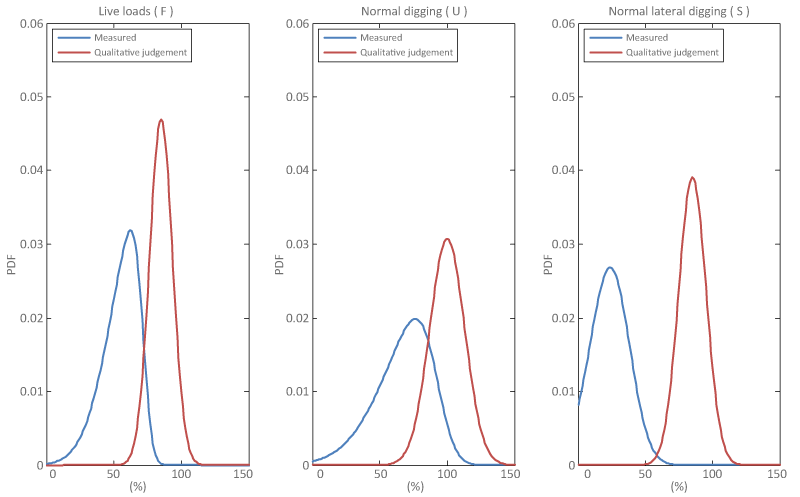
Figure 2: Comparison of Probability Density Functions for F, U, and S obtained from Measured Data vs AS4324.1-2017 Values
[1] Won-Hee Kang, Centre for Infrastructure Engineering, School of Computing, Engineering and Mathematics, Western Sydney University, Penrith, NSW, Australia. Email: W.Kang@westernsydney.edu.au
[2] Kang W. H., Uy B., Hawkes D., and Morgan R.: Reliability analysis for load factors in steel bulk material handling structures with respect to AS4324. 1. Australian Journal of Structural Engineering, 17(2): 99-108, 2016.