At the recent ASEC Conference, ASPEC Director Richard Morgan shared an important update on the forthcoming AS 4324.1 revisions, the Australian Standard that underpins safety and performance for materials handling structures. With improved guidelines for handling extreme weather, load requirements, and structural resilience, the revised standard reflects the latest in safety advancements for equipment like stackers and reclaimers. Read on to learn more about the significant changes in AS 4324.1 and how they will impact the future of materials handling safety.
On October 30, 2024, ASPEC Director Richard Morgan addressed the ASEC Conference to discuss the upcoming updates to Australian Standard AS 4324.1. These revisions bring new considerations for safety and resilience in the design of materials handling structures, including stackers, reclaimers, and ship loaders. Marking three decades since the standard’s initial release, the 2025 revision introduces advanced guidelines that reflect both industry advancements and lessons learned from past incidents.
Key Revisions and Their Impact
The primary goal of the AS 4324.1 revision is to make these structures safer and more resilient. Here are some of the key changes:
- New Load Cases for Wind: The AS 4324.1 revision introduces new load cases for wind due to thunderstorms. This is crucial for improving the stability and safety of materials handling structures in extreme weather conditions. Thunderstorms can produce sudden, intense wind gusts that can catch machines off guard, leading to potential failures. By including these new load cases, the standard ensures that machines are designed to withstand such unexpected forces, thereby reducing the risk of accidents and improving overall safety.
- Simplifications and Clarifications: The standard has been simplified and clarified for suspension elements and hydraulic cylinders. Additionally, the steel material requirements have been updated to ensure better compliance and understanding. These changes make the standard more user-friendly, reducing the complexity for enxgineers and designers. Clearer guidelines help prevent misinterpretations that could lead to design flaws or safety issues.
- Materials Requirements: The revised standard allows automatic acceptance of steel conforming to AS 4100 or AS/NZS 5100.6, simplifying the materials requirements and ensuring consistency with other standards. This change streamlines the material selection process, ensuring that only high-quality, compliant materials are used in construction. It also reduces the need for additional testing, saving time and resources.
- Safety Factors for Suspension Members and Hydraulic Cylinders: The revision includes modifications to safety factors, allowing single suspension elements with a revised minimum factor of safety and specifying minimum safety factors for hydraulic cylinders in compression. This ensures that even if a single suspension element is used, it will have a high enough safety margin to prevent failure. For hydraulic cylinders, the specified safety factors ensure they can withstand the loads and stresses they will encounter during operation and extreme overload situations.
- New Load Case for Loss of Chutes: The inclusion of a new load case for the loss of chutes or telescopic chutes addresses potential risks and enhances the design’s robustness. Chutes are critical components in materials handling, and their sudden loss can destabilize the entire structure. By considering this scenario in the design phase, engineers can implement measures to mitigate the impact, such as reinforcing the structure or adding fail-safes.
- Resistance Against Drifting: The requirement for available drive force during driving against a relocation wind has been modified, maintaining a minimum factor of safety against drifting whilst allowing some over torque on the electric motors due to wind gusting effects. This change ensures that machines remain stable without oversizing the drive motors which would have flow on effects to other load cases such as buffer impact and travel device obstructed.
Learning from Past Failures
One of the critical aspects of the revision is learning from past failures. Machine structures have shown higher failure rates compared to static structures. A notable failure occurred in Western Australia in the early 1990s, where a bucketwheel reclaimer’s shaft fractured, causing the machine to collapse and resulting in a fatal accident. This incident led to a coronial inquiry and the publication of the original AS 4324.1 in 1995. In the preparation of the original AS4324.1- 1995 and in subsequent revisions, the committee has introduced load cases based on known causes of failures.
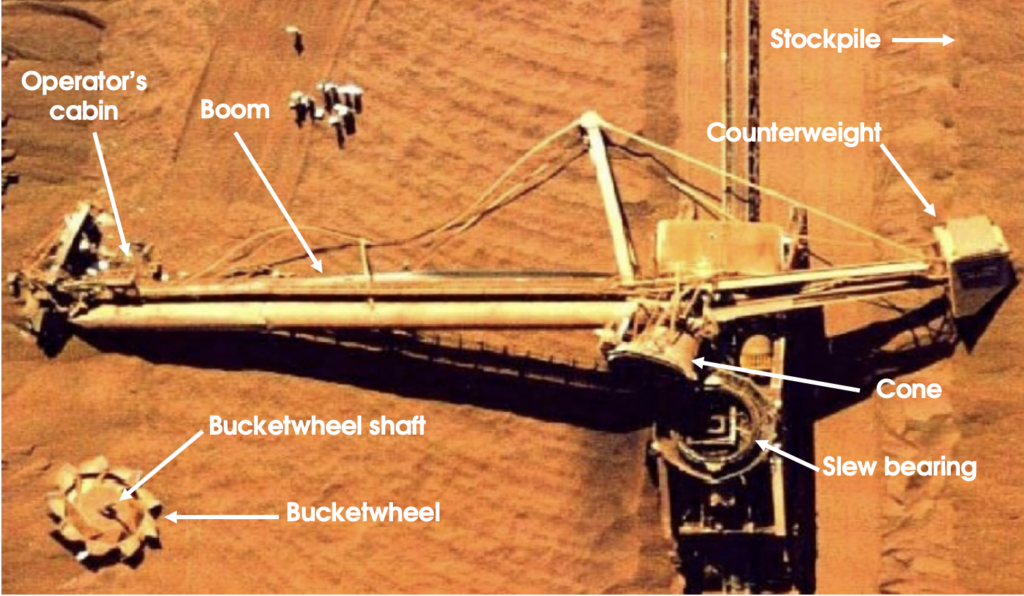
Wind Loads and Operational Protocols
The current protocol for dealing with wind loads involves stopping operations at defined wind speeds (20-22 m/sec), relocating to a storm tie-down location (30-33 m/sec), and resisting ultimate design wind in tie-down configuration (over 60 m/sec in cyclonic regions). The revision also considers thunderstorm wind loads, providing detailed wind speed vs. time data to ensure comprehensive safety measures.
- Operational Wind Speed: Machines are designed to operate safely up to a certain wind speed, typically 20-22 m/sec. Beyond this, operations are halted to prevent accidents.
- Relocation Wind Speed: When wind speeds exceed the operational limit, machines are moved to a storm tie-down location where they can be securely anchored. This relocation wind speed is usually higher, around 30-33 m/sec.
- Ultimate Design Wind Speed: In the storm tie-down configuration, machines must be able to withstand the maximum wind speeds expected in the region, which can exceed 60 m/sec in cyclonic areas. This ensures that even in the most extreme weather conditions, the machines remain stable and secure.
- Stranded from Tiedown Case: One of the significant additions in the revised standard is the load case for machines “stranded from tiedown.” This scenario addresses situations where a machine cannot be relocated to its storm tie-down location in time due to sudden, severe weather events like thunderstorms. In such cases, the machine must be able to anchor to the rails at any position along the track to withstand the wind forces. This ensures that even if a machine is caught in a storm without being properly tied down, it can still remain stable and secure, preventing potential catastrophic failures.
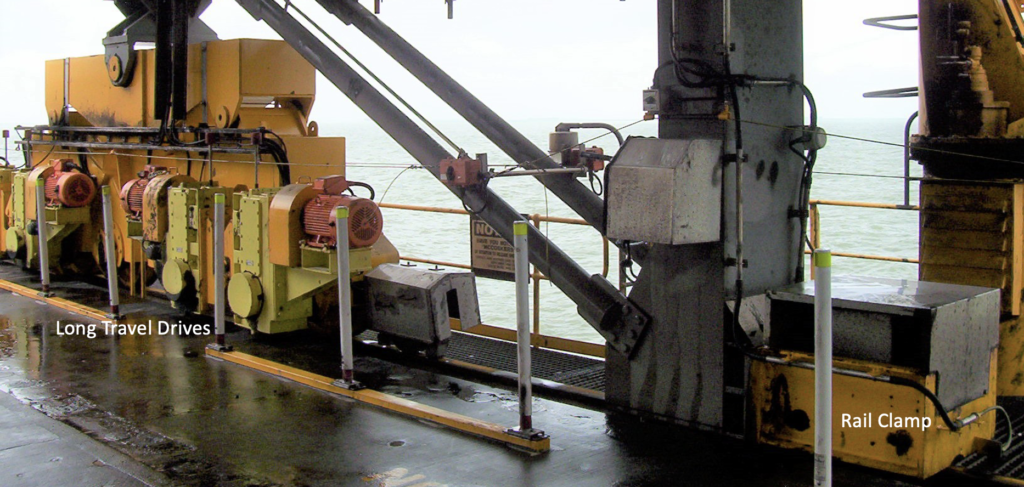
Conclusion
The revision to AS 4324.1 is a significant step towards improving the safety and reliability of materials handling structures. By addressing historical failures and adapting to evolving environmental conditions, we can ensure that these structures remain robust and efficient. I am excited about the positive impact these changes will have on the industry and look forward to the release of the revised standard in 2025.